We are proud to announce that from the start of 2021 all Loading Systems dock levellers will be in powder coated condition.
We are unique in providing such a high-grade protective coating to our dock levellers. With powder coating we have elevated the quality level of our dock levellers which brings us ahead of the competition.
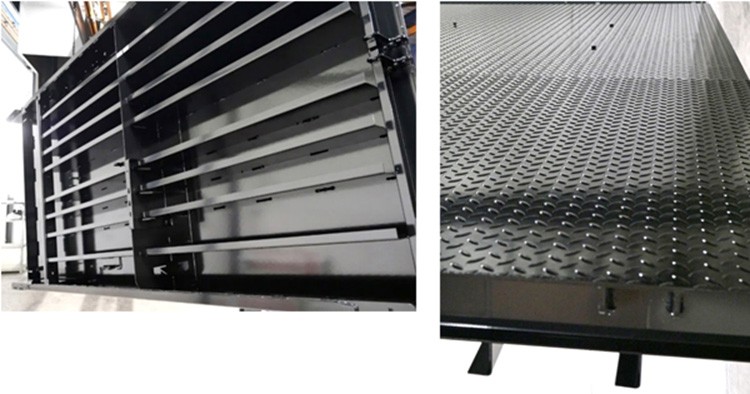
What is Powder Coating:
Powder coating is a modern ecological technology of surface treatment of metal products. The powder used in this process is a mixture of finely ground particles of resin, pigment and additives. This mixture is electrostatically sprayed onto the surface of the product to be coated, where the charged powder particles adhere to the electrically grounded surfaces. After application of the powder, the products enter a curing oven where, with the addition of heat, the powder chemically reacts and fuses into a smooth coating with high cross-link density. The result is a product with a uniform, flexible and durable high-quality coating and an attractive finish.
We have tested several different powder coating materials to compare their protective capabilities and select the best material for our application. This has resulted in a powder coating material with an optimal mix between corrosion protection (salt spray test), QUV resistance (to weathering), impact resistance and adhesion performance.
The level of protection against corrosion that we are able to achieve in our new powder coat shop by applying a single layer of 80 micro meter is a so called C3 category protection. By applying a second layer we achieve protection against the most severe C5-I category, which equals a product remaining corrosion free for 1000 hours in a salt water bath.
Main benefits of using Powder Coating as painting process:
- Durability: Powder coating provides a more durable finish than liquid paints can offer, while still providing an attractive finish. During the curing process at high temperature, the powder will form chemical bonds leading to a flexible but durable finish. Powder coated products are more resistant to diminished coating quality as a result of impact, moisture, chemicals, ultraviolet light, and extreme weather conditions. In turn, this reduces the risk of scratches, chipping, abrasions, corrosion, fading, and other wear issues.
- Safe for the Environment: The technology of powder coating is considered to be environmentally safe. While liquid finishes contain solvents which have pollutants known as volatile organic compounds (VOC's), powder coating contains no solvents and release negligible amounts, if any, VOC's into the atmosphere.
- Efficiency: Because of the electromagnetic energy used to apply the powder to parts, and the filtering of wasted powder for re-use, there is almost no waste in the powder coating process. Additionally, our experts can apply as much powder as necessary in one application. Due to the short drying time and with no flash off period required, another layer of coating can be applied right away without obstructing the production process. This second layer results in a C5 quality.
- Variety: Powder coating has a huge potential for customisation of the product finish. Besides the ability to produce any colour, we can also select from a range of premium finishes.
- Easy Maintenance: Powder coating is highly durable, so it lessens the chances of corrosion occurring. Products will require less maintenance work to keep them in optimal shape.
If you would like further information on the above or any of our products please Contact us